So much to report on...so slack at reporting! I know it's been a long while folks but, hey, I been building a house! Taking time out to rest the weary body today I found the following that I wrote some months ago. So, here is finally an update of sorts:
 |
mudder's little helpers |
+++++++++++++++++++++++++++++++++++++++++++++++++++++++++++++++++++++
With the bales all firmly in place and trimmed to suit, it was time to squeeze 25mm conduit (for electrical feeds to GPOs embedded in rock walls) into the straw. Out came the little chainsaw again to chase grooves into the straw bales then I used more fencing wire pins to keep the conduit in place. This will keep the conduit and associated cabling clear of the mud render. I tried to keep bends in the conduit to as wide a radius as possible as this will assist in pulling cable through later on.
 |
conduit |
Because the fire rating of our place (BAL29) mandates windows made of metal, metal reinforced uPVC or fire resistant timber we had to make a choice. Steel, alloy and uPVC all look a bit icky to us, so we went with timber. Ony 7 timber species have been tested and approved for use in BAL-29 areas. These are:
Blackbutt
Spotted Gum
Silvertop Ash
Kwila (Merbau)
Red Ironbark
River Red Gum
Turpentine
Merbau was struck straight off the list (and if you have to ask why, check this out:
merbau==BAD) and we hunted for the closest source. I found Red Ironbark harvested (sustainably!) within our Shire boundaries and, after many hours doing take-offs to work out quantities, put in an order. Besides, we'd already drooled over the Red Ironbark windows produced by
Paarhammer and loved the grain on this wood. Unfortunately, Paarhammer's stunning windows exceeded our budget by many tens of thousands (try $100k+), so I'm resigned to becoming a fine joiner overnight and spending many weeks (months??) sanding, shaving and shaping super-dense hardwood. Already running several weeks late, our timber supplier cocked up the shipping and sent it via Tasmania. Ooops, there go the carbon miles. Not only that but somehow 2/3 of the shipment never made it to us! So, the timber man mills up some more and then goes and loses that too! Third time lucky...
Needless to say, I dont think that we can advertise this guy too much!!
 |
window timber - part 1 |
While I was waiting for our window timber to arrive, I had to move on to other tasks. Schedule duly juggled, we had local plumber Josh Bell visit and finish off the roof flashing. He also installed 30,000L of catchment tanks below the house and we ran lines up to the header tank site. Next job was pouring a slab for this header. Smart money would say: form it up, install the reo-mesh and bring in a mini-mix. Being not so smart (and trying to save money wherever possible), I let Dana convince me to mix this lot onsite in the trusty concrete mixer. It took us over 10 straight hours to mix and pour this lot. I recovered in a only a day or so, but it took Dana weeks to get over the hurt. Next time we'll consider the cost-benefit ratio of a mini-mix a bit more carefully!
Josh soon came back to hook up the header tank and fill it with ballast (water) so that we didn't lose yet another tank to the 'installation-art-gods'. About 30 minutes into filling this big guy (24,000L), the fire pump (only $45 at a clearance sale) gave up the ghost. Bugger. A quick spin into town sourced a hire pump so that we could at least get a few thousand litres in the header and sleep easy knowing that it wasn't going to get airbourne.
 |
let's catch our water |
 |
Josh- "I glue pipes" |
Still waiting on the final window timber, I made a start on the solar power system. We'd sat down a long time ago to work out our usual power consumption in Melbourne and come up with a conservative figure of 5kWH per day. I re-checked the figures and they seemed good (leaving some headroom for stay indoors winter days), so started shopping around for an installer. I have a few friends who do grid-connect systems but we've been quoted $35k to pull power to our boundary. With another 150m to get to the house and hook it up and quarterly bills for ever, this was out of the question. I sourced quotes from far and wide but we decided to keep it local if possible. The estimates received were all within 20% of each other so it came down to sorting through fine technical discrepancies and individual company approaches. We ended up settling on using the guys from
Sun Real and not only because they are also keen Frank Zappa fans. I'd had glowing reviews from several people that had used them and they've been at Stand Alone Power Systems (SAPS) for 15+ years. So, no 'Johnny-come-lately' riding on the the crest of the greenwash wave but proper 'alternative' guys with a long track record.
Before the Sun Real team could get started, I had to do a few things. First off was building concrete plinths to mount the panels on. The aesthetics committee had won out over the technically easier approach of roof mounting panels. Scrounging and saving where ever possible, I used bits of scrap to make the formwork for the ground mounts. A few sheets of formply would have been heaps easier then cobbling together offcuts and rejects but more $$$$ out the door. This DIY approach meant lots and lots (and I mean LOTS) of bracing. This took several days to get robust enough.
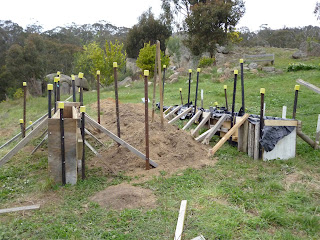 |
plinth forms |
 |
bodgy but strong |
Next step was trenching for cabling between panels and electrical cabinet (located on the nook at the South of the house) and cabling back out to the outside points and backup generator. A few painful hours on the shovel highlighted the need for more mechanical toys. Back off to the hire shop to grab a trencher!!! No need to Dial-Before-I-Dug because I knew exactly where the underground hazards were. Unfortunately, I vagued out and went straight through the stormwater pipe we'd laid only weeks prior. What a silly boy! Oopsies...:)
 |
even with safety tape @400 deep |
 |
sooo much easier than by hand |
Next, I had to lay and glue HD conduit @ 600mm deep; backfill for 200mm; lay electrical underground warning tape; further backfill to ground level under infill slab where battery box is located; and finally, dig out, construct formwork and install reo for this slab. By now being as wise as the ancients, a mini-mix was ordered. Funky local organic baker mate Sim found a morning to help barrow and pour the muck. Apart from the truck driver insisting that we were at least 1/2 metre short on quantity we had fun. Thanks heaps fella. Besides, we got it all done (sailing a little bit too close to the wind) with 1 whole shovel full left over. I must be getting good at this takeoff caper!
 |
plinths curing |
 |
back door slab |
+++++++++++++++++++++++++++++++++++++++++++++++++++++++++++++++++++++
Of course, if you've been following via
The Owner Builder, you probably already know all this and more. :)
<<Pix later...when I find time>><<HEY, I found some time...:)>>
<<And maybe even some more words..maybe.>>